This article discusses the latest trends in space electronics, its demand, and challenges in the NewSpace market.
It also provides an outlook on the innovative solutions in the global space market, by Texas Instruments, a paying participant in the satsearch membership program.
Further, the article also provides a brief outlook on power management systems and the Texas Instruments’ strategy for the NewSpace market. The piece was developed in collaboration with the Texas Instruments team – Michael Seidl, Aerospace systems engineer, and Adrian Helwig, Aerospace field applications engineer.
Introduction
Space programs heavily depend on reliable and efficient power systems. Everything from operating sophisticated instruments to basic life-support systems for astronauts relies on the availability of electric power. Always available, always within spec. In this article, we’ll delve deeper into these vital systems, starting from power generation and storage, to power distribution and finally, the point of consumption – the Point of Load (PoL).
The most common power source in satellites is solar panels, which typically generate an output voltage ranging from 100V to 200V. This is then stepped down to a battery charging voltage of 24V to 70V. Power distribution, regardless of the battery voltage, typically occurs at 28V using a buck/boost DC/DC converters. For each submodule or subsystem, the main voltage rails, ranging from 28V down to 12V, 5V, -12V, -5V, and so forth, are isolated. Finally, we reach the PoL stages, where voltage can be as low as 0.8V for FPGAs, though 3.3V is more common. Please note that these are typical values, and while there is no existing standard yet, we anticipate the introduction of such standards in the near future.
Generating and managing power in space is no small feat. The process is fraught with challenges. Power generation in space is costly, considering the size of the solar panels, the complexity of unfolding mechanisms, and weight-related issues. When on the ‘dark side’, energy must come from the battery, which again brings up the challenges of weight, size, and cost. The absence of air in space means no convection; all heat must be radiated away, leading to significant costs in cooling efforts.
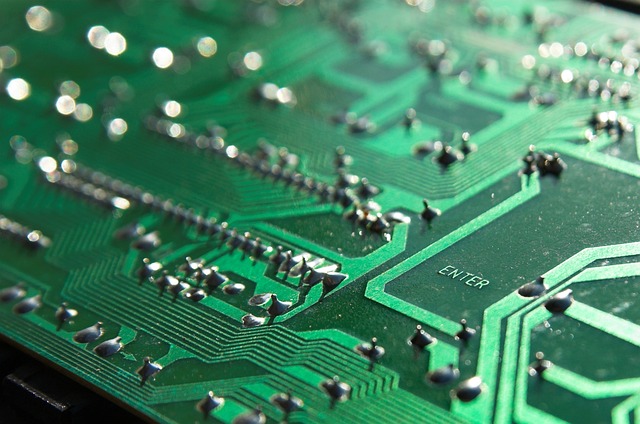
Add to these challenges the harsh environment of space: high radiation levels that vary with different orbits; extreme temperature cycles, with Low Earth Orbit (LEO), experiencing multiple transitions from the sun to darkness each day; and high vibrations during launch. Despite these challenges, humanity’s drive to benefit from its installations in Earth’s orbits propels ongoing innovations in space electronics.
The emergence of the “NewSpace” industry, characterized by an increasing presence of private sector investment and innovation, has introduced a fresh dimension to the space sector. Traditionally, government-led space initiatives have focused on a range of objectives, from scientific discovery to establishing critical infrastructure for navigation, telecommunications, and military surveillance. Now, with the advent of NewSpace, these core objectives are being pursued alongside the development of profitable business models, introducing a new set of challenges and considerations.
Private investment in space missions necessitates a delicate balance between risk and cost
Power management systems in NewSpace vehicles need to provide full functionality while maintaining cost efficiency, a critical aspect in a market-driven sector.
When designers have to select their components the first factor is the mission profile, which takes into account radiation hardness. Single Event Effects, dependent on the orbit, along with the Total Ionizing Dose—essentially, the aging effect, dependent on both the orbit and mission duration—play crucial roles here.
A second, equally critical aspect is the temperature profile. In LEO, this is more severe than in Geostationary Orbit (GEO) due to multiple temperature cycles per day, which makes material usage extremely important.
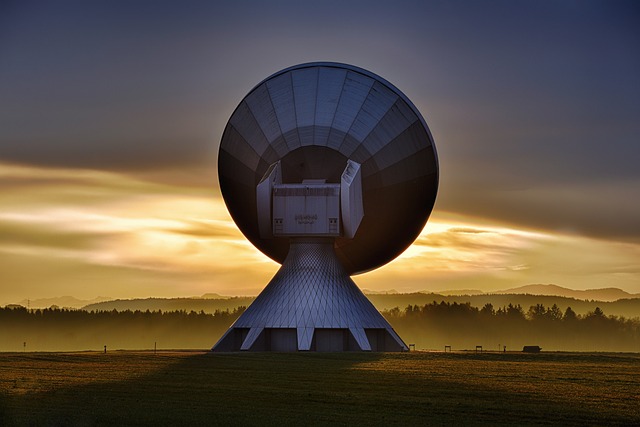
Designers have multiple options. On one end of the spectrum, we have the Qualified Manufacturers List Class V – Radiation Hardened Assurance (QMLV-RHA) according to the United States military specification MIL-PRF-38535. Due to the complexity of designing, manufacturing, and testing these devices, they command a premium price when required by a mission. These parts are offered in a highly robust ceramic package.
On the other end, up-screening of Commercial Off-The-Shelf (COTS) products is typically not advisable. These often lack testing programs, especially for complex products. Power products in COTS grade rarely exhibit good radiation performance (high current-carrying transistors show gate rupture effects). Moreover, COTS use materials not intended for space and show failures due to tin whiskers or bonding wire breaks, for instance. The mold compounds can outgas and cause damage to other sub-systems of the satellite, particularly any optical implementation.
A middle-ground solution is the Space Enhanced Plastic (SEP) with a reduced radiation hardness of typically 30krad, 43MeV. This offers a good compromise between cost and risk of failure. The radiation reports are readily available, and the material set is appropriate for space.
Once the right quality class has been selected, designers need to look at the functionality itself. Perhaps one of the most essential aspects to highlight here is power density, a concept that is particularly significant in the NewSpace market for several reasons:
- First, the pursuit of higher efficiency. Efficiency, in this context, refers to the ratio of the output power (useful power) to the input power. The higher the efficiency, the less energy is wasted, which in turn requires less energy to be produced. Notably, high efficiency means less power is needed for cooling, a significant advantage in space where heat dissipation is challenging.
- Second, power density involves leveraging this higher efficiency to reduce the board space and bulkiness of passive components, thereby saving further on costs.
The power system does also play a pivotal role in protecting devices downstream, especially when components with lower radiation hardness are used downstream. In the absence of radiation-hardened and cost-effective alternatives, Commercial Off-The-Shelf (COTS) high-performance processors or FPGAs, commonly used in other sectors, become sometimes the only viable options for NewSpace projects. The rapid detection of latch-up events (radiation-induced malfunctions in semiconductor devices) and power cycling of the affected device becomes a very critical function the power system must then provide. Furthermore, given its full dependency, the power tree must be extremely robust, especially considering that high current-carrying transistors can show gate rupture effects under heavy radiation.
In essence, the quest to optimize power in electronic space systems involves a delicate balancing act that requires us to continuously navigate a complex field of options, risks, and trade-offs. Therefore, the marvel and complexity of space exploration, are a testament to human ingenuity.
Enhanced on-board processing capabilities present new challenges for power supply solutions
In the evolving technological landscape, a significant uptick in on-board processing capabilities, complemented by the adoption of complex software systems, is redefining power supply requirements.
Consider the communication payload of LEO constellations. More processing power is now dedicated to data routing, and the replacement of conventional mechanical antenna pointing systems with electrically steered antennas requires even more computational power, not to speak about high-speed data converters that run meanwhile at 10 GHz and above which allow to skip the need for an intermediate frequency even up to the X-Band but produces a just incredible amount of data which all need to be processed, of course.
Further augmenting these systems are artificial intelligence or machine learning capabilities, enhancing the ability to determine optimal routing and network load options. Or, on-board pre-processing for optical and radar imaging payloads is lowering data rates, despite a concurrent increase in resolution. Additionally, due to the prevalence of space debris, autonomous maneuvering is becoming a requisite for collision avoidance.
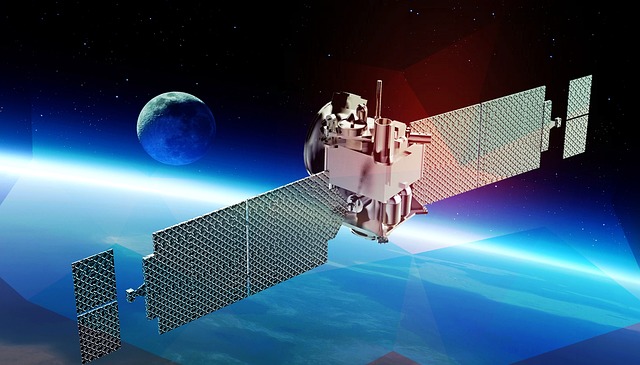
These advancements trigger a rise in computational power and complexity, highlighting the importance of software and the usage of processors or Field-Programmable Gate Arrays (FPGAs) that incorporate numerous CPU cores.
This transformation, however, introduces new challenges. The power tree, for instance, now requires increased power. The most recent and high-powered FPGAs demand high currents at incredibly low voltages, such as 0.8V core voltages with tens of Amperes. With a tight tolerance of +/-3%, we’re left with mere millivolts of wiggle room. This scenario accentuates the importance of efficiency and power density, particularly for these high current requirements, yet also requiring very high precision at the same time.
In conclusion, the ongoing progression of computational power in space has significant implications for power supply requirements. It necessitates superior current capabilities with exceptional radiation performance. The next-generation power supply must respond adeptly to load steps up to 100A, even at voltages as low as 0.8V, while maintaining high power density and accuracy. While these demands pose considerable challenges, they simultaneously unveil new avenues for innovation within the technology domain.
Innovating solutions for the NewSpace market from Texas Instruments
The challenges of the NewSpace environment are numerous and multifaceted. As one of the leaders in the tech industry, Texas Instruments has been actively and proactively adapting to these challenges.
A significant part of Texas Instruments’ strategy includes a broad product range catering to various current levels, with some components handling up to 18A per component and capable of being paralleled to achieve more than 100A. To ensure the finest level of precision, Texas Instruments has introduced unique precision capabilities.
The company has also incorporated numerous protection features, such as overcurrent (OC), overvoltage (OV), under-voltage lockout (UVLO), and over-temperature (OT), including auto retry capabilities. This comprehensive protective setup greatly enhances system reliability and resilience.
Recognizing the diverse needs across different space missions, Texas Instruments offers three space-grade quality classes. The QMLV-RHA class is designed for traditional space, GEO and deep-space missions, and human space missions, offering radiation hardness of 100krad, 75MeV. The SEP class is intended for NewSpace and LEO constellations, providing radiation tolerance of 30krad, 43MeV, at a cost-effective price point. Lastly, the brand-new QMLP class offers radiation hardness similar to QMLV-RHA but with a pin-compatible plastic package to SEP. Texas Instruments played an active role in developing the QMLP standard, ratified in November 2022, with the first QMLP release expected shortly and several more planned within the year.
These offerings are designed to provide mission flexibility, allowing one R&D investment to be easily adopted across different missions. It also simplifies the introduction of new products with similar performance, using the same or very similar package as industrial versions.
A key part of Texas Instruments’ solution, especially for the power tree, includes redundancy, where units are galvanically isolated from each other to prevent fault propagation. The Fault Detection, Isolation & Recovery (FDIR) capability is another crucial feature that provides integrated diagnostic, monitoring, and protection features, alert signal generation, an enable pin, and a current limit function. Load switches and eFuses are employed to offer solutions for full disconnection when needed or to limit inrush current or peak voltages to avoid unnecessary stress on any components downstream. Digital isolator products complement the FDIR solution catalog.
Small and micro-satellites: catalysts for innovation in space power management systems
The NewSpace industry is experiencing a noticeable trend toward launching small- or micro-satellites. But, what does this mean for power management systems in space? Can this shift drive innovation and streamline power management processes?
Signs point towards an affirmative response. The industry is already talking about standardization efforts, with models like SpaceVPX or Advanced Data Handling Architecture (ADHA) gaining traction. These standards propose a modular and exchangeable design, thereby enhancing redundancy and enabling the sharing of computational power. The benefits are manifold: costs are reduced, volumes are increased, and R&D efforts can be reused, creating a more efficient and productive environment for semiconductor investments.
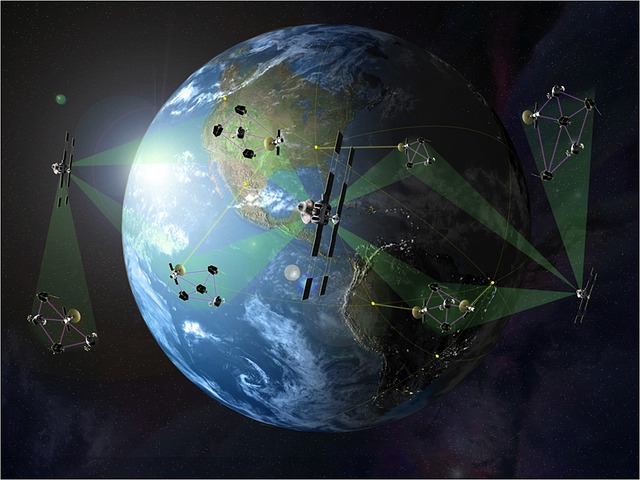
A clearly defined power supply definition can help streamline optimization in terms of cost and performance. Recognizing these evolving dynamics, Texas Instruments closely follows these activities, aiming to deliver optimized products that meet the high volume expectations of the expanding small- and micro-satellite market.
Specifics concerning power supply, such as voltage and current levels, are vital considerations. Additionally, protection and robustness, along with fault detection and reporting capabilities for recovery, are integral elements of these innovative power management systems. These features echo the reliability and safety measures found in other industries, such as automotive, implying that the space industry is aligning with terrestrial technology sectors to optimize systems and procedures.
In conclusion, the shift towards small- and micro-satellites does appear to be catalyzing innovation in power management systems in space. By embracing standardization, reusing R&D, and prioritizing key performance metrics, companies like Texas Instruments are well-positioned to meet these new challenges and contribute to the NewSpace era.
Texas Instruments strategy for the emerging space market: new products and partnerships
Serving the emerging NewSpace market requires constant innovation, adaptation, and a commitment to delivering cutting-edge products. Texas Instruments demonstrates this dedication with numerous new product releases every year, and the numbers continue to grow.
In 2022, a series of power-centric product releases hit the market, broadening the company’s offerings and providing advanced solutions for the fast-growing space industry. These include Load Switches such as TPS7H2221-SEP, which is radiation-tolerant with a 1.6-V to 5.5-V input and 1.25-A current capabilities.
Switching Regulators, such as TPS7H4003-SEP, provide radiation-tolerant 3-V to 7-V, 18-A, synchronous step-down conversion in a small space-enhanced plastic package. Texas Instruments also launched Linear Regulators, including TPS7H1210-SEP, offering radiation-tolerant, -3-V to -16.5-V input, 1-A adjustable output negative LDO linear regulator in a plastic QFN package.
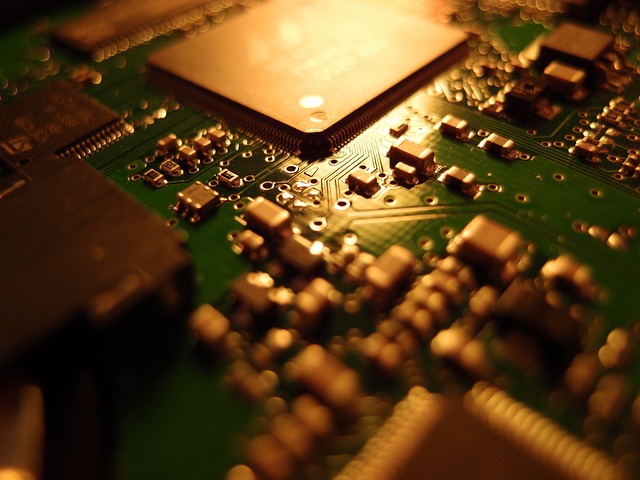
Furthermore, the company has rolled out a new PWM Switching Controller family with eight devices for different topologies and mission profiles. The superset devices include TPS7H5005-SEP and TPS7H5001-SP, offering radiation-tolerant and radiation-hardened, 2-MHz, dual-output PWM controllers with synchronous rectification and dead time control.
Beyond individual components, Texas Instruments emphasizes comprehensive solutions via reference designs. A dedicated reference design team, known as Power Design Services (PDS), works on numerous existing and upcoming designs for various topologies and power levels. These designs can be readily accessed on the Texas Instruments website.
Additionally, the company is actively fostering third-party collaborations and partnerships. This includes cooperation with Star-Dundee on a SpaceFiber design with TI power, and Teledyne e2v’s DDR4 memory incorporating TI power and terminators. AlphaData’s space-grade development design based on Xilinx KU60 also utilizes TI components for core supply, auxiliary rails, and memory termination. This approach has been successfully replicated for their latest Versal platform.
In conclusion, Texas Instruments’ strategy for the emerging space market is multifaceted. TI will continue to extend its wide array of products at different quality classes to help designers meet their performance and cost goals. Innovation efforts focus on efficiency and power density, supply rail quality, and accuracy while assuring the highest level of robustness and reliability, including support of effective recovery strategies to meet FDIR requirements. TI strives to provide very strong technical support via its e2e forum or its collaterals such as reference designs including test reports, application notes, and more. Last but not least, TI puts a strong focus on availability in terms of easy ordering, and fast delivery thanks to a healthy inventory level, and a strong long-term supply commitment.
To find out more about Texas Instruments and for more information on its product and services portfolio, please view the company’s supplier hub on satsearch.