This article discusses some of the most common criteria to consider when selecting propulsion solutions for space systems and the advantages of Field-Emission Electric Propulsion (FEEP). It also features FEEP products from ENPULSION.
In this piece, produced in collaboration with propulsion solutions provider for ENPULSION, a paying participant in the satsearch membership program, we highlight some of the most important advantages of FEEP using solid metal indium as a propellant, which is one of the most advanced propulsion technologies on the market and has gained considerable flight heritage in recent years.
Introduction
The propulsion systems form an important part of the space systems to create mobility for a variety of functions such as orbital maneuvering, docking with the space station, orbit transfer, etc. While several different propulsion systems such as chemical, electric, and solid systems are categorized generally for space systems, the electric propulsion system is one of the most commonly preferred systems for satellites or spacecraft.
Electric propulsion utilizes less propellant as compared to other conventional propulsion systems. This leads to an increase in the spacecraft velocity and provides more efficiency in the overall operation of the propulsion system. Since the inception of NewSpace technology, research and development have advanced in the electric propulsion segment; Leading to the rise of more variety of electric propulsion systems in the market. Enpulsion’s propulsion products, based on Field-Emission Electric Propulsion (FEEP) technology, are one such unique innovative entry into the market. In the next part of the article, we will provide an outlook on FEEP, its advantages, as well as take a deeper look into its applications.
What is FEEP?
The FEEP is an electric propulsion technology, that has been developed for more than 30 years and had its first successful In-Orbit-Demonstration in January 2018. Since then, it has gained a considerable amount of flight heritage and currently close to 200 thrusters based on this technology are in orbit, with an accumulated on-orbit operation of more than 150 years.
Inside a FEEP thruster, the solid metal propellant is liquified in orbit, and a strong electrostatic field extract ionizes and accelerates the propellant from the ion emitter. By changing the field’s parameters, thrust and specific impulse can be varied as required. The ion emission is supplemented by electron emission from neutralizers to maintain the charge stability of the spacecraft. The emitted propellant is replaced in a fully passive manner by capillary forces which maintain the propellant supply from the propellant reservoir up to the emitter tips, relying on the surface tension of the propellant itself. A FEEP thruster, therefore, does not require any external forces like pressurization or pumps. Furthermore, the FEEP system is fully solid and inert during ground handling, integration, and launch. Indium is a key solid metal propellant that is used in the FEEP. In the next section, we will take a deeper look into why Indium is important as a solid metal propellant for FEEP.
Why indium is used in the FEEP?
Some of the most highly-advanced FEEP emitters use indium, a non-toxic, non-reactive, and non-radioactive metal as a propellant, with negligible evaporation even in a vacuum at high temperatures. The FEEP thruster technology is an entirely passive system using no hazardous materials and an unpressurized solid propellant during all process stages.
Even when active, no part of the thruster is pressurized, and no leak is possible. This technology does not generate any debris even in case of disastrous events on the spacecraft level like micrometeorite impact or collision. Since the propellant does not store chemical energy or is pressurized, physical damage/unforeseen full loss of power will lead to solidification of the propellant, (as opposed to an explosion), it is therefore self-passivating. This means that no explosive reaction can harm the spacecraft system and no additional launch preparation and safety requirements are needed.
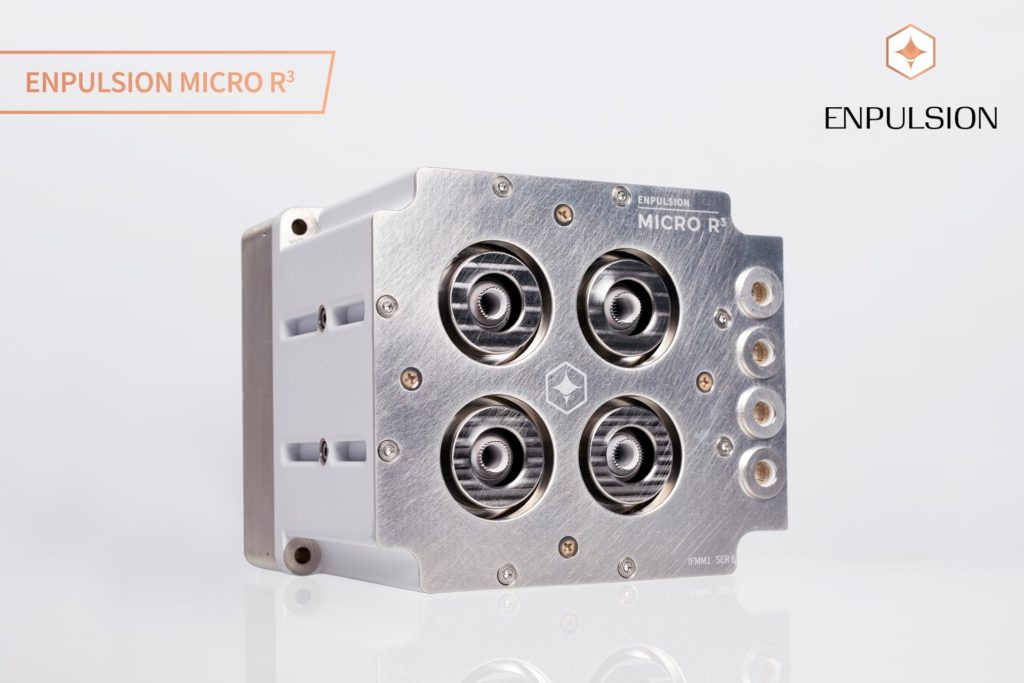
FEEP thrusters are delivered with propellant tank subsystem and propellant included, and in a ready-to-fly state and are designed for simple and fast integration. Many propulsion systems using other propellants have to be shipped empty and filled at the launch facility, introducing additional expenses and procedures, with propellants having to be purchased separately, often at considerable cost.
Indium is non-toxic and easy to handle. It is stored unpressurized and, unlike high-pressure tanks, it does not need special authorizations (launch waivers) to be launched as secondary payloads, and is RoHS and REACH compliant.
FEEP advantages in a nutshell (part 1)
- consists of fully integrated system
- propellant tank subsystem INCLUDED
- propellant INCLUDED
- thrusters shipped in ready-to-fly state
- simple and fast integration
- non-toxic, non-reactive, non-radioactive
- NO additional welding required
- NO additional tanks required
- NO filling operation required
- NO moving parts
- NO pressurized components
- NO chemical energy stored
- NO additional launch preparation
- NO additional safety requirements
When to use FEEP?
With a FEEP propulsion system, thrust can be controlled through the electrode voltages, providing excellent controllability over the full thrust range down to a precision of a few tens of µN, as well as low thrust noise. Due to the efficient process in which up to 60% of the evaporated indium atoms can be ionized, FEEP emitters can provide a very high specific impulse and can accurately control the ISP anywhere from 1,000s to 6,000s.
Advanced FEEP thrusters can be used as compact pre-qualified building blocks in order to provide custom solutions at a commodity price and ultra-short lead times. Although the building blocks are completely self-contained propulsion systems, the whole cluster can be operated as a single plug-and-play unit.
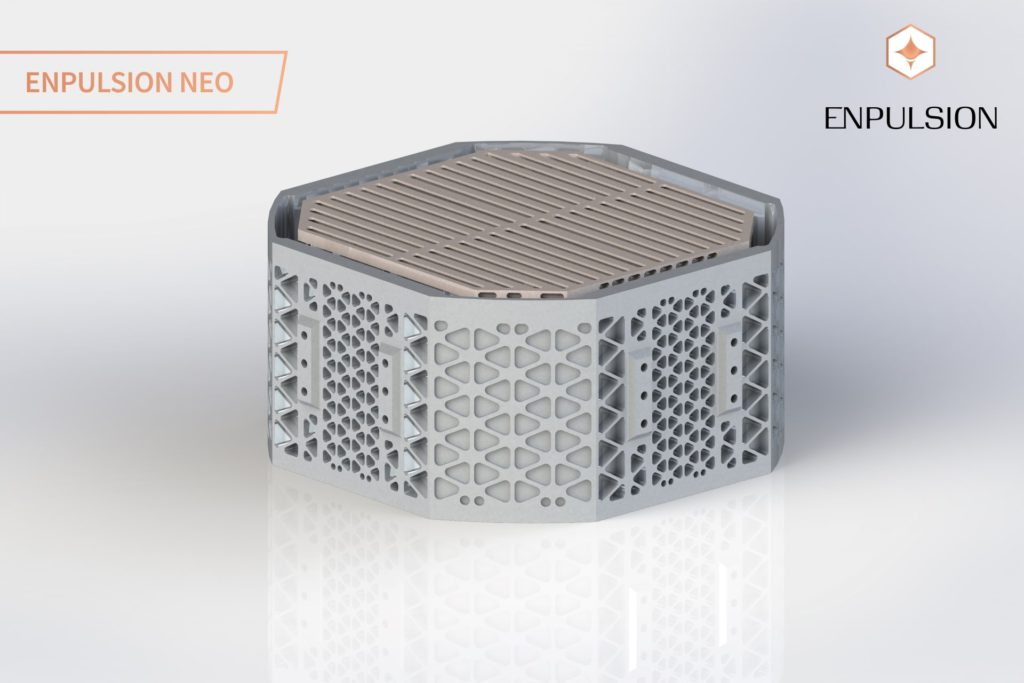
Available FEEP propulsion systems show that this technology can be used on a wide range of spacecraft. Fully integrated FEEP propulsion systems can have outside dimensions starting below 1U with a (wet) mass of only 900g (eg. ENPULSION NANO). In contrast, larger thrusters operating at total system power of up to 800 watts can be used to move satellite mass of up to 500kg per thruster with multiple thrusters per satellite being able to maneuver even satellites with a mass of up to 2.000kg (eg. ENPULSION NEO). Some of the unique properties of FEEP that make it the most suitable for maneuvers and other space operations include:
- station-keeping
- orbit control
- orbit raising
- orbital transfers
- formation and cluster initiation and control
- end-of-life deorbiting
- the high Specific impulse (ISP) makes FEEP also particularly suitable for exploration and even deep space missions
FEEP advantages in a nutshell (part 2)
- considerable flight heritage
- very compact design
- high performance & low complexity
- unmatched controllability
- very high precision
- low thrust noise
- hot standby mode from which full thrust can be reached almost instantaneously
- the ability for continuous thrust over several months, or years
- very efficient process
- very high specific impulse
- designed as pre-qualified building blocks
- commodity price
- ultra-short lead times
FEEP has Hidden costs and additional services
When compared to other propulsion technologies, there might be additional operations and preparations required, that have to be taken into account as “hidden costs” – which primarily include health and safety requirements in handling the propellants. Some of them come at considerable effort and cost which are not needed for a FEEP propulsion system.
FEEP advantages in a nutshell (part 3)
- NO simulant loading & draining needed
- NO separate delivery of propellant needed
- NO additional regulatory compliance needed
- NO issues with storage and transportation
- NO additional safety equipment needed
- NO hazardous and potentially dangerous operations needed
Some of the following operations could also lead to a considerable amount of effort and additional costs. Considering these factors carefully could be beneficial for the overall operations and safety:
- integration & testing processes
- regulatory compliance
- cost of storage and transportation
- launch campaign support
- post-launch LEOP
- IoT support
- test facility design, engineering, operation and maintenance
- hot firing and environmental test execution
- propulsion testing from component to systems level
- launch support at spaceports
- propellant supply and delivery
- ground support and safety equipment
- making hazardous operations safe
Conclusion
When compared to other propulsion technologies, FEEP has unique advantages such as making integration as simple as bolting the thruster head and electronics on their respective panels and connecting the harness – with no additional launch or safety requirements, making the fully integrated FEEP propulsion system essentially a plug-and-play component.
The development of the ENPULSION NEO thruster is the latest addition to a wide range of available propulsion systems, that can cover small and mid-sized satellites but also large satellites of up to 2.000kg launch mass. With its high specific impulse (>2500s) and propellant density 4 times higher than xenon the ENPULSION NEO thruster system is both more compact and lighter than traditional electric propulsion systems.
Development and qualification of the ENPULSION NEO thruster are supported by the European Space Agency (ESA) through the ARTES program. Qualification of the thruster system is scheduled to start in early 2024.
To find out more about ENPULSION and for more information on their product portfolio, please view the company’s supplier hub on satsearch.