This article is a reproduced version of a piece originally published on NanoAvionics.com – you can view the original article at this link.
The miniaturization of many aspects of space technology has been a clear trend in recent years. However, the choice of overall satellite size is a decision that should be driven by individual mission requirements, rather than any outside industry pressures.
This article discusses some of the most important factors which can determine the ideal platform size for a small satellite mission or service’s constellation.
Before we dive into the details of how to select the right satellite platform for your application, let’s address some common misconceptions about the size of the primary payload being the determining factor of the satellite platform size.
The primary payload
There is often a misconception about payload size being the primary driver of a platform’s volume. For example, a new Earth Observation (EO) company developing their first system based on an imager of size 12U may expect to easily fit it into a 16U nanosatellite envelope.
However, for an effective EO satellite you need a lot more hardware than just the primary payload. There is power and thermal management equipment, solar cells/panels, batteries, attitude control, downlinking, on-board computers (OBCs) and processing systems, with associated memories, and more. This supporting hardware is just as critical for achieving mission objectives than the main camera.
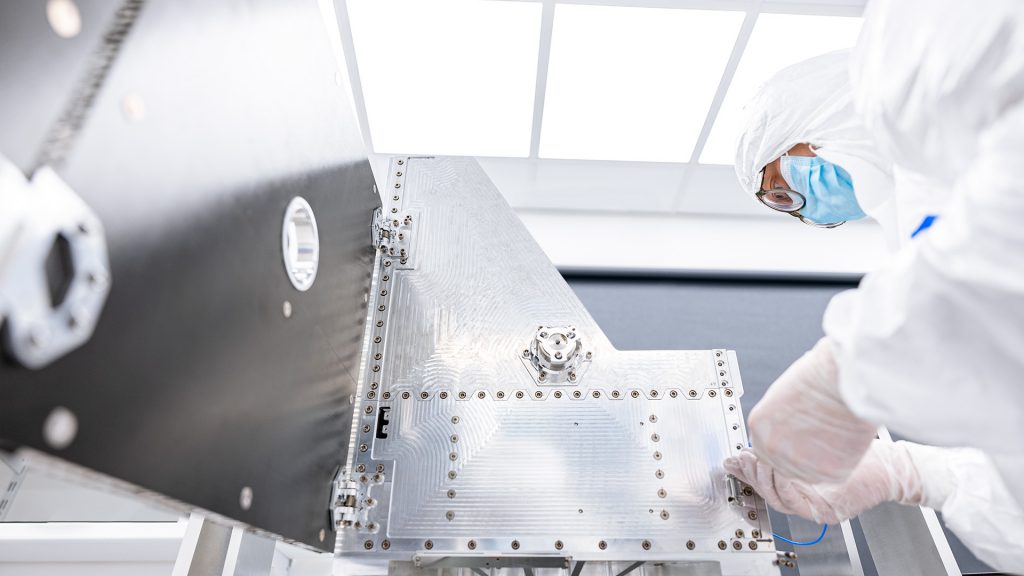
In some ways, primary EO payloads in satellites are analogous to digital cameras or smartphones. To get a high-quality image on a regular camera a good photographer will make use of various pieces of supporting equipment. This might include a tripod, a range finder, a larger lens, an external flash, filters, mounting pieces, and even additional lighting. If the object of the image is moving, the camera will also need a stable sliding platform or rotating system to ensure sensitivity is maintained.
All of these auxiliary devices are analogous to the hardware supporting a primary EO payload onboard a satellite. And every new capability, mission requirement, or performance target can result in additional subsystems that need to be installed onboard – each taking up mass and volume budget.
In addition, if you want to take the highest quality images possible with a camera on Earth, you need to take a lot, select the best, and post-process them effectively. This might need computing and/or external storage devices, along with the required cabling and power resources to facilitate them.
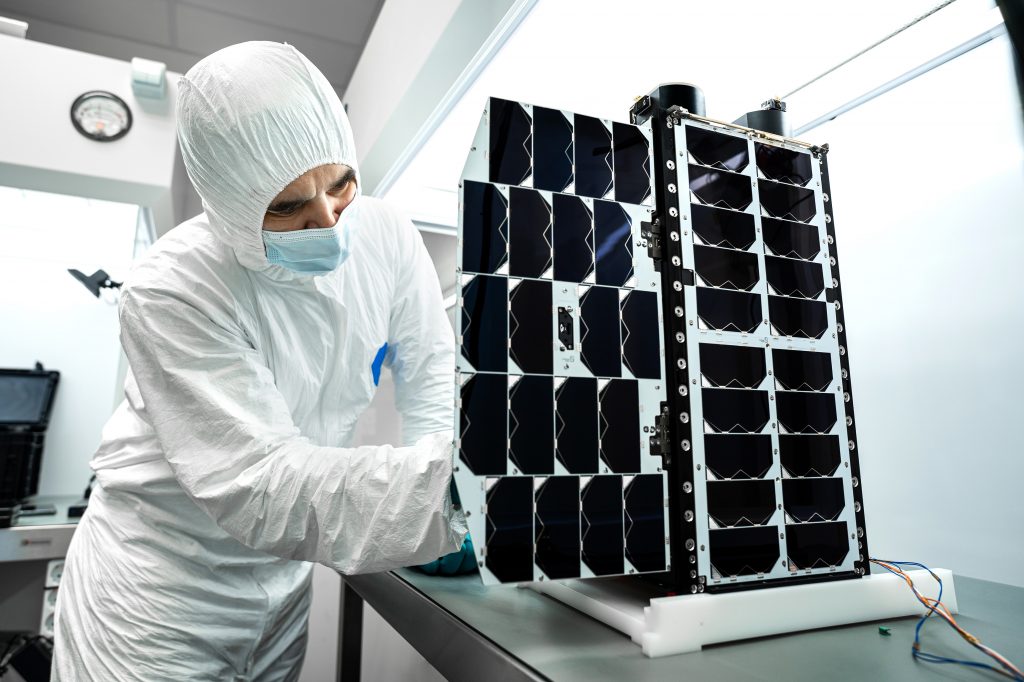
The same is true on a satellite. Significant advancements have been made in the area of on-board data processing (OBDP) and artificial intelligence (AI) in recent years that have added new capabilities to mission operators.
But higher processing capabilities typically require more power, greater satcom capacity (due to the increased tasking and control demands, as OBDP enables operators to capture data on more targets with each pass), and possibly additional thermal management. All of these factors can result in an increase in the amount of hardware required.
It is of course possible to run a satellite payload with a very basic system setup, but the total performance that results is a fraction of what can be achieved if the rest of the platform is scaled up. In today’s competitive industry high-quality data is expected, so a minimal system is unlikely to be the best business decision.
Performance over hardware
In order to avoid biasing system selection by focussing solely on the primary payload, mission designers should instead carry out first order assessments based on the required levels of performance. As discussed in the previous section, this entails making judgments about the supporting systems for the main payload as well as the payload itself. The functionality of such supporting systems is typically classified as follows:
Power requirements – e.g. solar cells and panels, batteries, the Electrical Power System (EPS), thermal control, and connecting and management hardware.
Positioning, pointing accuracy, and agility – e.g. the Attitude Determination and Control System (ADCS), reaction wheels, magnetorquers, propulsion (and associated propellant storage and management), and all of the interfaces and connected devices.
Processing and data storage – e.g. the On-Board Computer (OBC), payload processors and On-Board Data Processing (OBDP) systems, Command and Data Handling (C&DH) system, memory, data interfaces, and other control software and hardware.
Downlinking and communication – e.g. antennas, radios, communications systems, and associated power and control hardware.
Redundancy – e.g. redundant subsystems, and/or extra power budget margins, etc.
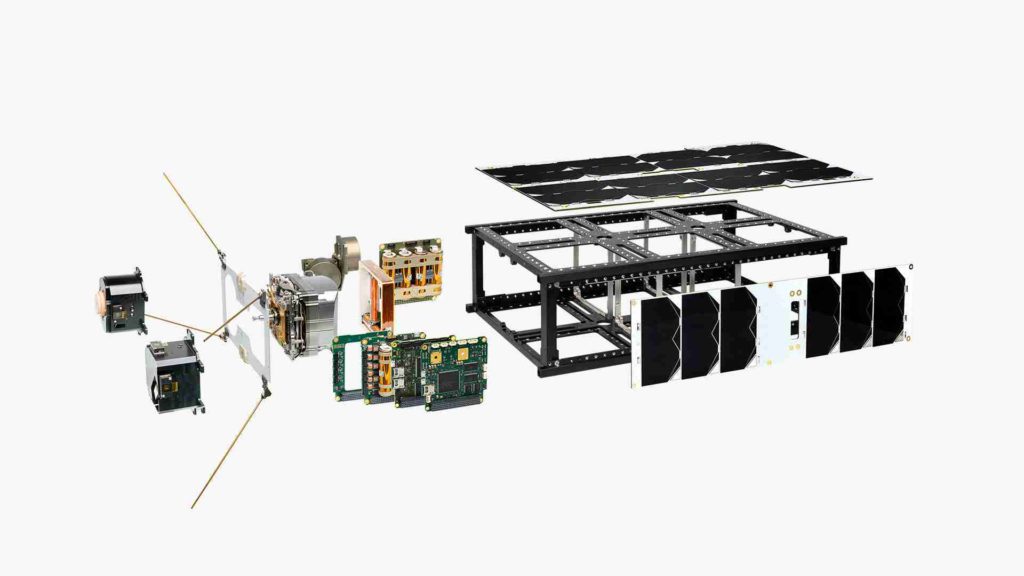
It is important to consider the idiosyncrasies and trade-offs of such hardware when planning a volume budget. For example, larger subsystems are likely to require more power but usually have better thermal management than smaller equipment.
In communication satellites higher power radios can be particularly bulky and the main antenna itself can play a significant factor in the choice of platform size. For lower radio frequencies, despite needing less power, the antenna needs to be larger for precise signals – particularly if a deployable system is used.
All such choices can be simplified when the required satellite performance is treated as the major determining factor in a system’s design. However, there are some factors that don’t have a material impact on the choice of platform size.
Engineering considerations
A larger platform does not necessarily mean a more complex system. If the primary and supporting payloads are scaled up in order to achieve higher performance, a larger platform may feature a similar number of connectors and interfaces as a small volume system.
In addition, larger platforms are much easier for engineers to work with. They can be manipulated, constructed, de-constructed, and tested faster and with fewer resources. It is also easier to deal with thermal hot spots in a large system because components can be packed in less closely, packed more strategically, or utilize active thermal management systems, which are harder to fit the smaller the satellite.
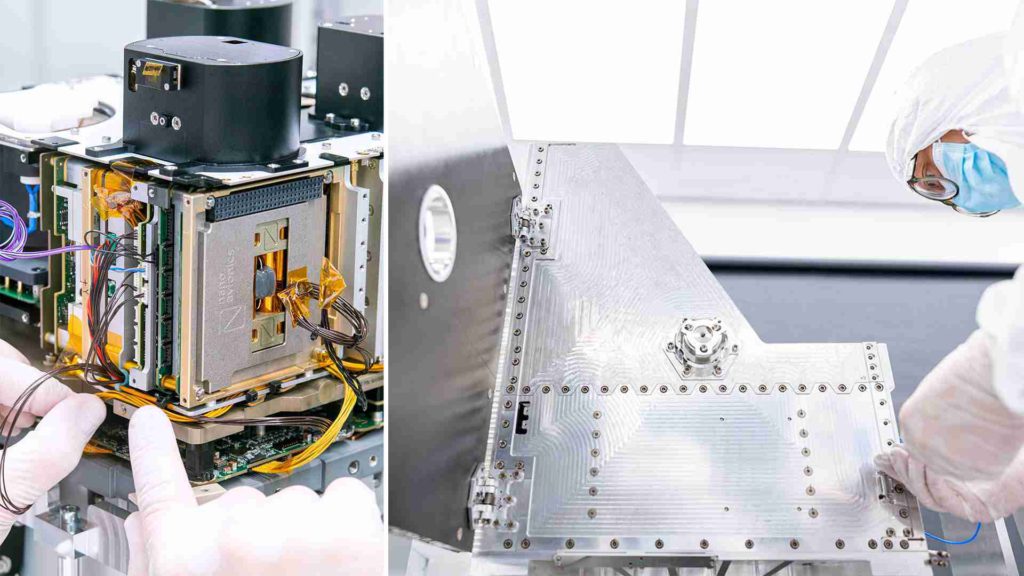
A bigger system provides more flexibility and more room for sophisticated design requirements. For example, for a high-resolution imaging payload there would be little space on a 16U platform for larger reaction wheels, which limits the satellite’s maneuvering abilities.
In comparison, a NanoAvionics MP42H, featuring larger reaction wheels, would have a higher slew rate and would be able to image more targets during the same orbit. The MP42H could also include larger solar panels with more solar cells, drastically improving the payload’s duty cycle.
Combining just these two improvements could deliver multiple times more imaging opportunities during every orbit, leading to an increase in significant revenue. The price increase from an M16P to a MP42H is not significant, so the potential RoI is much greater.
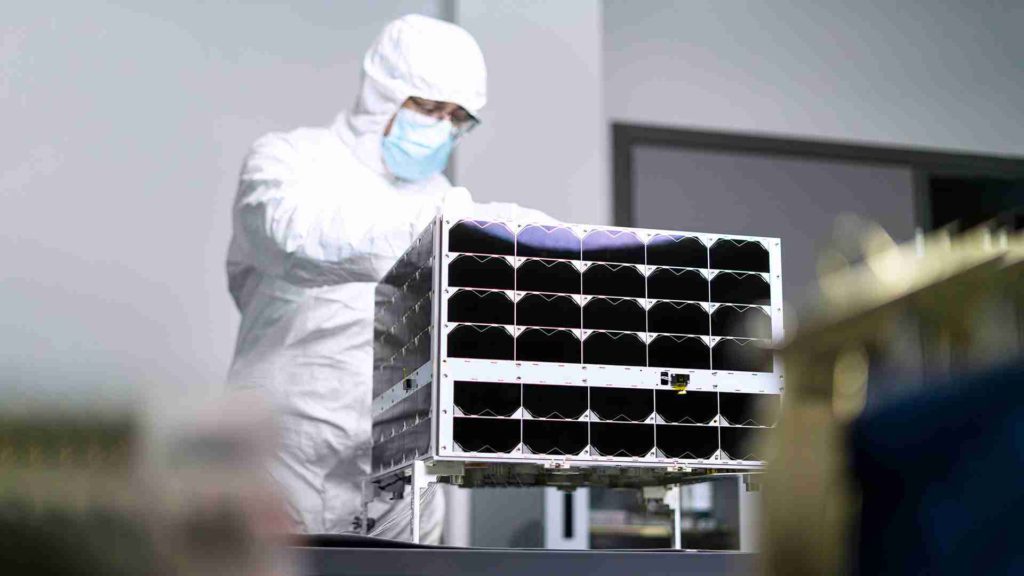
In addition, for engineers assessing 6U options note that an 8U is also an extremely viable alternative. The NanoAvionics 8U nanosatellite (M8P) bus can provide very similar average orbit power to a 16U nanosatellite, and improve mission capabilities and redundancy at only marginally increased production and launch costs compared to the M6P.
The only potential mitigating factor is the availability of deployers. 8U satellites are far less common than 6U systems, so there may only be a few options available for the satellite’s deployment after launch.
To scale up further, in comparison to an 8U system, the NanoAvionics 12U platforms have inter-satellite links for regular connectivity and Albedo-free Fine Sun Sensors. A star tracker and Inertial Measurement Unit (IMU) are also integrated, while these systems are optional for 8U buses.
The 16U platform has the same architecture as the 12U but offers greater orbit average power and a higher battery capacity, resulting in a significant performance difference for missions that require higher duty cycles.
Finally, NanoAvionics’ microsatellite buses are also higher in performance than all nanosatellite buses. Not only is there much more space for additional hardware but the payload controller and power systems are also more advanced than the nanosatellite platforms to cope with the expected performance requirements.
The full mission plan
For commercial entities the mission plan is developed in order to meet the required performance levels specified in the business plan – as discussed earlier. The mission plan itself determines the system requirements and drives the platform size selection.
For example, if a large number of maneuvers (or a small number of extensive maneuvers) are required during the mission, the satellite has a higher delta-v requirement. This will require more powerful propulsion subsystems and therefore a bigger platform.
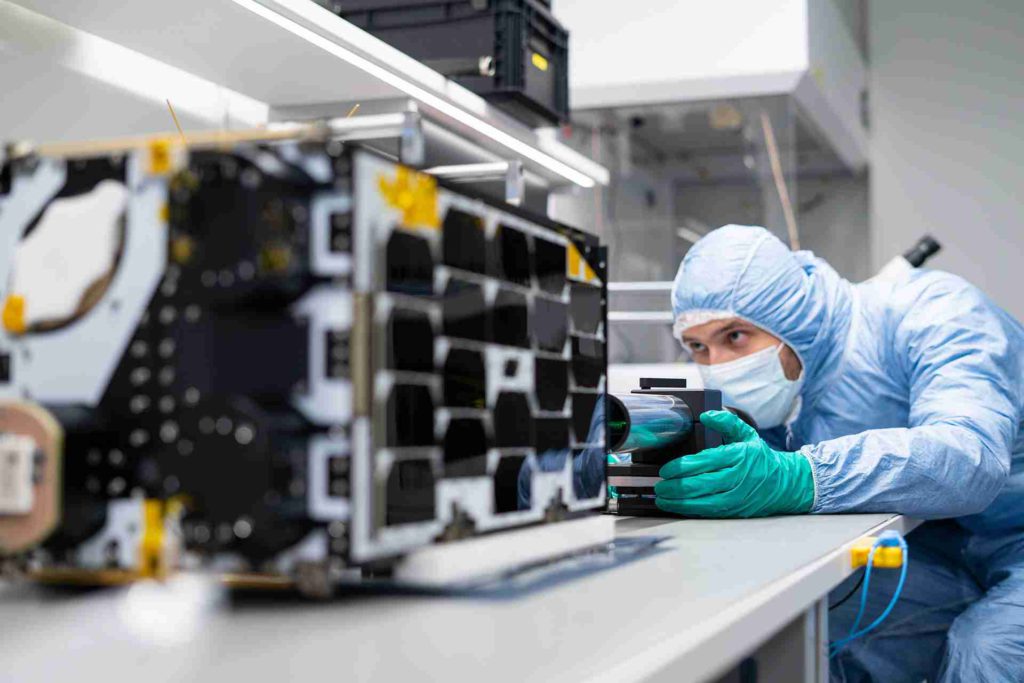
The choice of launching a single satellite or a constellation of satellites also makes a significant difference on the choice of platform size. A larger, more multi-functional satellite, with in-built redundancies, is recommended for single-satellite missions, as defined by the required service level and accessibility needed.
In a constellation it is possible to share tasks and resources, so multiple smaller platforms are more viable. Each satellite can support the other systems’ performance (e.g. re-imaging a location, backing up data, managing the processing, optimizing downlinks and ground station passes, offering some redundancy if one system fails, etc.) so smaller, less powerful, systems are an option.
In addition, with the current changes in guidelines and policies around space sustainability and debris, it is recommended that newly planned satellites evaluate propulsion systems or other technical solutions to enable end-of-life deorbiting maneuvers.
This might be another reason why a platform should be scaled up. A very simple propulsion unit might take up just 0.5U in volume, but won’t offer enough longevity for complex operations and emergency maneuvers to avoid collisions, followed by de-orbiting to scale up. The choice of de-orbiting strategy might require larger subsystems and the supporting components to power and use them.
The mission plan, and associated contingencies, will dictate many of the hardware and software choices of a satellite. But it is important that an accurate cost determination is made in order to ensure that the plan can be fully funded.
Costs and budgeting
In recent years a number of the costs associated with building, launching, and operating a satellite have come down, opening up new opportunities for both research and commercial mission. Nevertheless, budget is still one of the most important factors to consider when selecting a satellite platform size for any mission. In general, larger platforms will be more costly, but it is important to consider all aspects that go into this determination, such as:
Engineering time and resources – the technical aspects of developing a system – discussed further in the next section.
Launch and deployment options – while costs don’t differ much, availability for launches of satellites of different sizes can be variable. And a delay in launch means a delay before revenue generation can begin.
Return on Investment (RoI) – larger satellites can provide higher volumes of more valuable data, meaning the potential RoI that can be achieved can justify the larger upfront investment.
Ongoing operations – once a system is in orbit there are various ongoing costs that need to be factored into the overall budget such as ground station subscriptions, licensing renewals, data handling, storage, and security costs, staffing (including employment and training of replacements if needed) and so on.
Single vs. multi-satellite missions – it can be possible to achieve economies of scale in some areas when launching a constellation. This can bring down the overall mission budget and enable investment in larger, better performing satellite platforms that will generate more commercially valuable data.
Risk appetite – it is important to remember that, in space, nothing is certain. Risks are always present and should be carefully weighed up in all financial decisions.
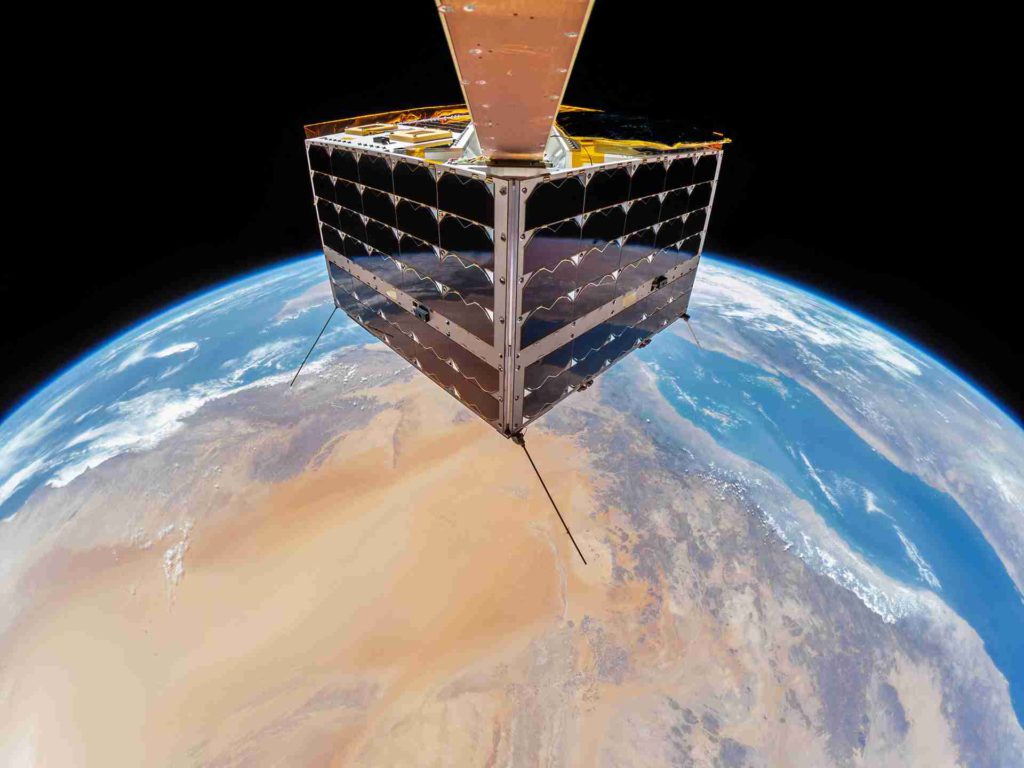
Budget constraints affect every project, particularly in space, but having a holistic approach to satellite and mission design, considering RoI alongside initial and ongoing outlay, can help make development decisions easier. And engineering is an important aspect of this.
What not to consider
In the first two sections of this article the hardware setup and primary payload were focused on, as well as the importance of considering performance. Achieving the target levels of performance also relies on the full mission plan, encompassing all elements of a system’s development, launch, deployment, and operation.
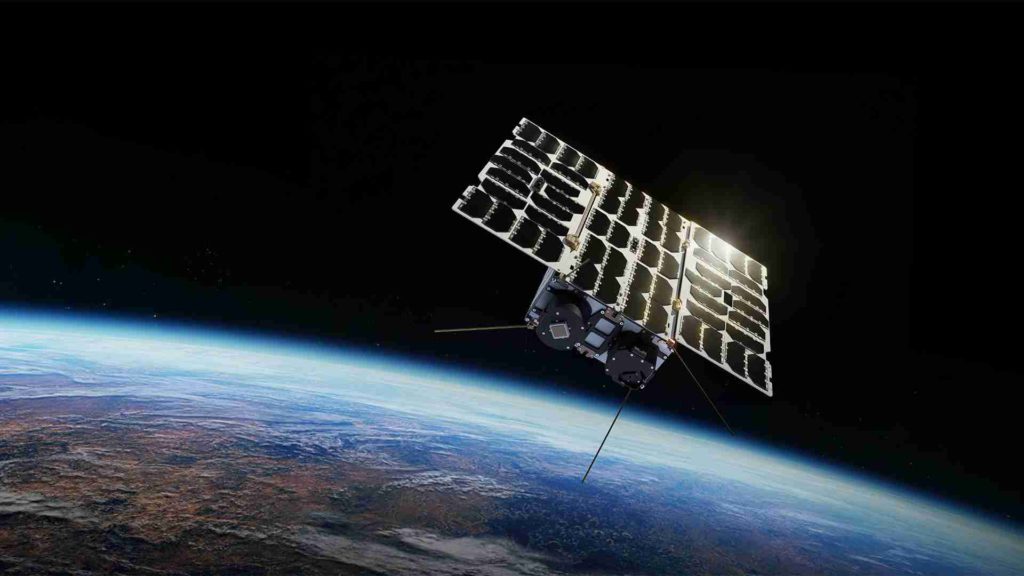
However, there are some aspects of this that have no real effect on the choice of platform size. These factors will be important when assessing costs and resources, but will need to be judged independent from platform size. Here are three key factors that don’t have a major impact on selecting a platform size:
Ground segment – in recent years innovation in the ground segment has led to a variety of new opportunities for mission designers. Managed networks offer flexible and affordable business models, new communications systems are providing higher bandwidths at lower costs, and software platforms are simplifying engagement with ground stations.
Logistics requirements – although a larger and heavier system would usually require a small increase in transportation costs, this is marginal compared to the overall price of a satellite. The space industry supply chain is developing rapidly and there are now many options for companies that need to move hardware between manufacturing locations, testing facilities, and launch sites, so logistics costs and resource requirements have little bearing on selecting platform size.
Aspects of licensing and compliance – satellite licenses are always an important aspect of any mission, particularly if the payloads are sensitive and/or military in nature. However, most compliance aspects relate to a satellite’s intended applications and use, rather than the system’s dimensions.
Conclusion
Selecting the right satellite platform for a new space mission or constellation is one of the most important choices that a team can make. The dimensions dictate the variety and quality of subsystems onboard, the applications that the satellite can perform, and, ultimately, the commercial value that the system can create.
The widely held notion of larger systems being unsuitable for economically-minded companies is no longer valid in today’s industry. Advances in equipment innovation and reliability, combined with decreases in launch costs make it more viable than ever to develop a larger, more adaptable system that can generate valuable data in high volumes.
Space is an increasingly competitive market and high quality data, with good availability and reliability, are now expected from commercial services. This requires larger, more power-hungry primary payloads and communications equipment, as well as the necessary supporting systems for them – all resulting in a larger satellite.
Versatility and redundancy are also increasingly expected, and in most cases the requisite levels can only be consistently achieved with larger platforms.
There is an ideal satellite platform size for any mission or service, which will deliver the best performance at the lowest cost for an individual application. Hopefully this article has armed engineers with the knowledge needed to make that determination much more easily in the future.
If you would like any further advice on which platform would best suit your needs, please contact Kongsberg NanoAvionics for a free mission questionnaire and to discuss your requirements.