This article is an overview of black coated space grade foils, covering the creation process, applications, and their importance in today’s space systems.
It also discusses examples of space missions, technologies, and projects that have utilized black coated foils produced by Acktar Ltd (ACM Coatings GmbH), a paying participant in the satsearch membership program.
Further, the article also provides a brief outlook on how the company envisions the future approach it will take for expanding production as well as research and development (R&D) capabilities. The piece was developed in collaboration with Acktar Ltd (ACM Coatings GmbH).
Black coated foils in space
Space systems are composed of several complex electronic, mechanical, and optical components. Each of these components is required to meet various space qualification standards, such as those provided by the European Space Agency (ESA) or the National Aeronautics and Space Administration (NASA), prior to their launch and deployment in Earth’s orbit, or beyond.
Black coated foils are used to enhance the performance of optical components while also providing a layer of protection for a variety of hardware in the harsh environment of space; to meet challenges such as:
- high levels of incident radiation,
- low external pressure,
- extreme temperature fluctuations,
- significant mechanical vibration/shock, and
- no possibility of maintenance or repair.
For example in space telescopes or optical systems, stray light can be generated from both intended and unintended sources. This can limit a telescope’s ability to detect far away signals and faint objects.
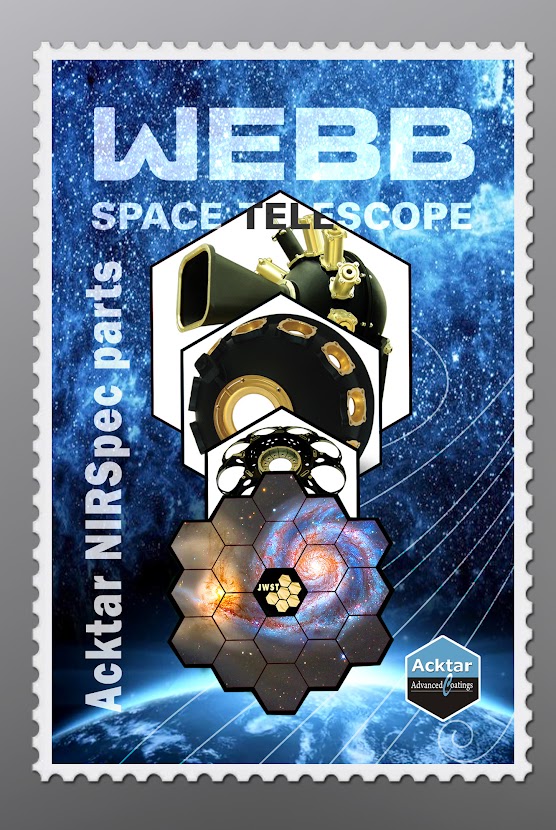
The detectors used in such optical instruments respond to the received amount of light. So in a small camera, stray light can cause a minor loss, but in a space telescope it can result in the loss of a massive amount of data potentially worth millions of dollars. It is therefore very important to correct and prevent stray light and minimize the chances of errors in optical instrument data.
Simultaneously, stray light is also responsible for a decrease in light absorbance ability and reduces the linearity of the instrument. Excess stray light in an optical system can also reduce the signal-to-noise ratio (SNR), which can result in a major degradation in performance; minimizing the amount and/or intensity of stray light striking the plane of an image can increase the SNR and reduce the noise.
A black coated foil can provide a surface that can significantly reduce reflected light by absorption. Therefore, black foils on such instruments not only improve their ability to reduce stray light but can also improve overall surface smoothness and resistance against corrosion.
Acktar has developed a range of specialized coatings and foils designed to enhance space systems in such processes. Before taking a closer look at these technologies, first let’s introduce the company.
An introduction to Acktar
Acktar Ltd. is headquartered in Israel with subsidiaries in Germany, Japan, and South Korea. Since its formation in 1993, the company has served a wide range of industries with its light-absorbing ‘ultra-black’ coatings. The German subsidiary ACM Coatings GmbH is not only responsible for the European marketing and sales activities but also converts Acktar’s coated foils into final products.
Acktar provides deep black coatings for light-trapping applications such as light baffles, ultraviolet (UV) sensors, passive infrared detectors, light detectors, UV absorbers, and similar components. Its coatings are space-qualified, inorganic, thin, and designed for low outgassing operation. They are also biocompatible and compliant with both the Restriction of Hazardous Substances (RoHS) directive and the Registration, Evaluation, Authorization and Restriction of Chemicals (REACH) regulation.
The company’s ultra-black coatings for space systems have become widely recognized in the space industry, primarily due to the advantages they can offer for protecting space hardware in harsh environments. For example, Acktar’s project experience includes:
- The James Webb Space Telescope (JWST) – on which Acktar provided black optical coatings of flight hardware for the Near Infrared Spectrograph (NIRSpec) – ‘Super-Eye’ instrument,
- ESA’s Copernicus Program – in which Acktar’s solutions were used in the UVN instrument on Sentinel 4, which observes atmospheric pollutants from outer space, and
- ESA’s Solar Orbiter (SolO) spacecraft – on which Acktar provided coatings for the Multi Element Telescope for Imaging and Spectroscopy (METIS) – a coronagraph used to analyze the Sun.
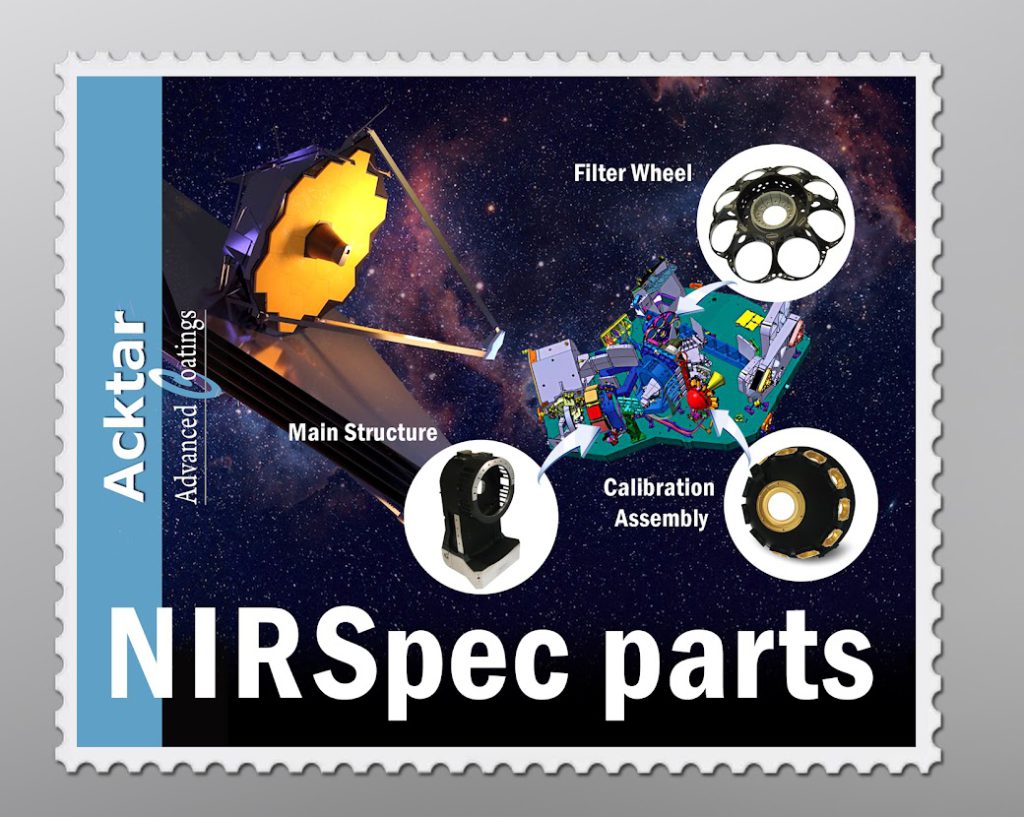
The company has also developed coatings and foils for various ranges of serially produced sub-systems, such as sun sensors and star trackers, for satellite constellations.
The proper functioning of electronic components in space is complex and difficult to maintain due to the bombardment of cosmic radiation; which can lead to both minor errors and major failures. Black coatings ensure components and systems are protected from such external impacts during operation in space.
Along with its various coating products, Acktar’s black foils are used to protect and enhance large areas and for contaminated environments where the light absorbing surface needs to be periodically renewed.
Before taking a closer look at the benefits that such foils can bring to space missions, let’s first review the manufacturing processes Acktar employs.
Acktar’s vacuum deposition technologies for space grade components
Acktar’s proprietary vacuum deposition (vacuum coating) technology generates unique coating surface areas designed for with exceptional characteristics. This approach produces results that Acktar have shown to be superior to those achievable by other processes, such as Plasma Electrolytic Oxidation (PEO), in a variety of important commercial applications.
Vacuum deposition is a process in which a thin layer of coating (typically a few microns in thickness) is applied to an object in a vacuum chamber. This is an inorganic, non-toxic, and environmentally-friendly process (with no aggressive chemicals used). It also enables accurate control of surface morphology to ensure the required radiation, optical, and physical characteristics are developed. Find out more here.
The company’s vacuum deposition technologies are unique in the sense that they can be applied to all space-grade components and materials. Acktar’s coatings can also be applied directly onto highly complex, 3-dimensional shapes and parts, which is particularly useful for areas such as cavities and inner surfaces that are used for defining and limiting the optical path of light.
The application of Acktar’s vacuum coatings technologies can lead to major improvements in a wide range of applications including, optical performance, solar energy, aluminum electrolytic capacitors, electronic enclosures, and heat sinks. Below are some of the main characteristics of Acktar’ coatings that lead to these changes:
- Uniquely large specific surface area combined with very small coating thickness – 2000 times the substrate surface in a coating only microns thick
- Close control of surface morphology – form and structure – for control of physical, optical and radiation characteristics
- Retention of substrate thickness and mechanical strength – specific surface coating technology rather than etching technology
- Vacuum coating operating at temperatures: -269°C to +350°C
- Adhesion to metallic and non-metallic substrates
- Mechanical strength and abrasion resistance
- Low outgassing
- Ecologically clean – no aggressive chemicals used
- Inorganic and completely nontoxic
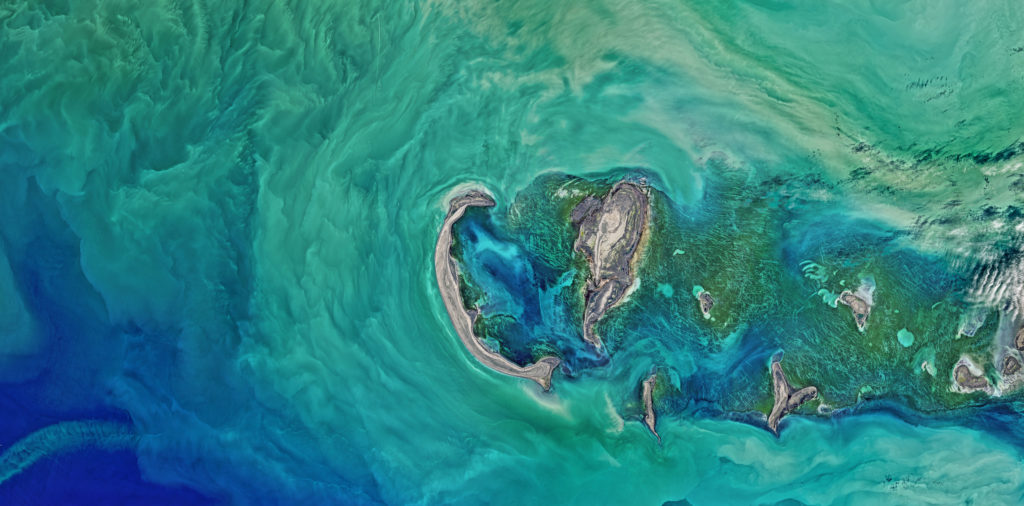
The development and delivery of black coated foils
As discussed above, Acktar’s inorganic coatings are fabricated using its proprietary vacuum deposition technology. Coating thickness mainly depends on the wavelength range of the customer’s mission requirements.
In applications such as Ultraviolet (UV), Visible (VIS), and Near Infrared (NIR), for example, the typical nominal coating thickness is below 5µm. If the project works in the far infrared (wavelengths from 5 to 14µm or beyond), the coating thickness will be below 15µm. The deposition process can be carried out at a wide range of temperatures, depending on the substrate.
A highly specific surface area coating can be created with a tightly controlled morphology to produce very low reflectance levels. By controlling the composition and morphology of the layered microstructure, the fabrication can be tailored to achieve the desired levels of absorption or reflectance over a wide range of wavelengths. The coating performance is also stable across a wide range of temperatures, which is particularly important for space applications.
The effort to produce a coating for customized space components and systems can vary from project-to-project. Because direct coatings are always customer-specific, each development is also treated individually.
Acktar exclusively carries out coating processes with its parent company in Israel. From the time the company receives an order from a customer until the delivery of the finished part, it takes an estimated six to eight weeks.
On the other hand, black coated foils are available in the form of a roll or sheet of material and can be delivered within 3-5 working days. Other forms of foils, such as cuts or die-cuts, are also available off the shelf, and can take 1-2 days more to deliver, depending on the customer’s mission requirements.
Black coated foils enable engineers to implement optical and radiation protection of their hardware without sending parts to Acktar for specialized coating. In addition, the black foil coating is also available either with or without an adhesive backing as sheets, die-cuts or rolls. This variety allows customers to apply the foils themselves to space systems in the most optimal stage of their mission’s development – with guidance from Acktar as needed.
The future outlook for black foils and coatings
As the number of space missions grows, and as more new innovations and applications are tested in orbit, there is a growing need to ensure high levels of optical performance through effective coatings and foils.
Acktar’s space portfolio already consists of projects such as the Characterising ExOPlanet Satellite (CHEOPS) mission and the space-based James Webb Space Telescope (JWST). Building on this proven track record of providing unique coating products and services to prestigious organizations such as ESA and NASA, Acktar is establishing itself as a well-known brand in this segment of the industry.
Acktar is also constantly expanding its research and development (R&D) and production capabilities to align with the evolving customer needs and market prospects. New missions are testing different optical setups and processes, requiring stray light protection and minimizing reflectance on complicated hardware components and surfaces. Acktar hopes to assist in such projects with new forms of black coated foil and coating products.
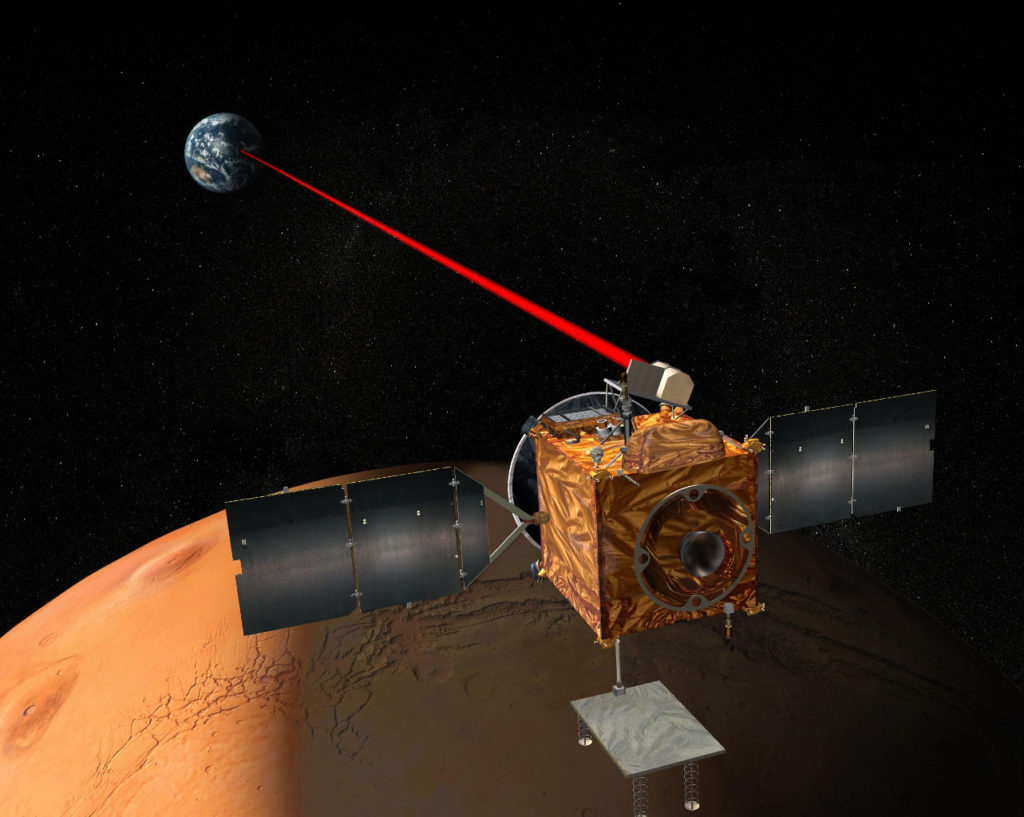
In addition, for passive thermal management of entire satellites, as well as for sub-areas and instruments, Acktar has developed new materials based on the company’s roll-to-roll coating technology. A thin film substrate, typically a polyimide such as Kapton, is coated with either Acktar’s deep black coating, which has a high emissivity and a high solar absorption, or with a white coating option, which has a relatively high emissivity but a relatively low solar absorption, in order to improve the passive temperature management of small satellites.
Driven by other developments in the industry, Acktar aims to enhance existing products and develop new lines to meet the changing needs of space engineers.
To find out more about Acktar, please view the company’s supplier hub on satsearch and you can also get more information in our podcast with Alexander Telle, CEO of ACM Coatings GmbH.